Category Archive: CNC Machining
Precision machining is a method of production that enables machinists to create detailed parts at incredibly tight tolerances. WIPCO has been producing precision-machined parts from some of the world’s most challenging materials, including super alloys, for two decades. Our expert machinists work closely with our customers to produce components crafted to the unique specifications of every project, no matter how complex. At our ISO 9001:2015/AS9100D-certified facilities, we are able to manufacture parts within tolerances of +/- 0.0002.
What is Precision Machining?
Precision machining describes the action of removing excess material from a large workpiece in order to shape it into a more precise part. This subtractive process enables machinists to adhere to extremely tight tolerances, even when working with very small components.
However, adherence to tight tolerances is not the only advantage of precision machining: It also offers a high degree of accuracy and repeatability when machining large quantities of the same component. This high level of accuracy is vital to numerous industries, as it ensures that minuscule parts will work seamlessly and interchangeably within larger machinery.
The tight tolerances of precision machining are made possible through the use of Computer-Aided Manufacturing (CAM) and Computer-Aided Design (CAD). Although many designs begin life as hand-drawn sketches, the incorporation of computer technology makes it possible for machinists to follow highly detailed blueprints when creating the final part. Designers create these blueprints as CAD files, which are converted to CAM files that can be read by Computer Numerical Control machine tools.
Precision machining is a subset of standard CNC machining. As the name suggests, precision machining offers tighter tolerances than standard CNC machining due to specialized tooling and additional process capabilities.
Precision machinists have an array of machining tools at their disposal. The ideal option will vary depending on the type of material being worked and the size of the final component. Machinists may work with any of the following:
- Drill presses
- Milling machines
- Lathes/turning centers
- Robotics
- Saws and grinders
Uses of Precision Machining
Precision machining is ideal when a design requires extremely tight tolerances that standard CNC machining cannot provide. Materials that precision machinists often work with, including:
- Aluminum
- Bronze
- Glass
- Graphite
- Plastics
- Steel
Although precision machining offers benefits for a vast range of applications, it is particularly advantageous for industries where the accuracy and precision of a part can mean life or death, such conditions found in aerospace or medical applications. Precision machining is often the production method of choice when manufacturing:
- Surgical instruments
- Aerospace components
- Solar and wind components
Although it can produce larger components, precision machining is also ideal in situations where many small parts must fit together tightly in order to function properly. This method of machining enables manufacturers to create incredibly small parts with extreme accuracy, ensuring that the components will function well when assembled together.
However, precision machining isn’t just used for the creation of new components. Many industries use this method of machining to repair tools and components that have been worn down with use. Precision machinists can sometimes recalibrate parts to bring machinery back to its optimal level of functionality.
Precision Machining From WIPCO
With its adherence to tight tolerances, high levels of accuracy, and ability to produce incredibly small components, precision machining offers immense benefits across a wide range of industries. At WIPCO, no project is too complex for our team of experienced machinists. We will work closely with you throughout the production process to ensure that your parts match your exact needs and specifications.
To work with us on your next precision machining project, contact us or request your quote today.
If your company needs precision machined parts, computer numerical control (CNC) machining services offer one of the most efficient means to get them. CNC technology provides cost-effective and accurate results on parts ranging from simple to highly complex. This guide will outline how CNC machining works, the different machining processes available, and examples of CNC machining use cases in different industries.
What is CNC Machining?
When it comes to manufacturing processes, there are three main categories to choose from:
- Formative manufacturing. Formative manufacturing forms an item from existing material without adding or subtracting anything. For example, liquid injection molding uses injects liquid plastic into a mold, where it hardens into the desired shape.
- Additive manufacturing. Additive manufacturing creates an item by layering materials on top of one another to create a specified shape. Examples include 3D printing and sheet lamination.
- Subtractive manufacturing. Subtractive manufacturing processes begin with a piece of stock material, then cut away material to create the design shape. Computer numerical control (CNC) machining belongs to the subtractive manufacturing category.
While formative and additive manufacturing processes are typically limited to certain types of plastics and polymers, CNC machining is compatible with a much wider variety of materials, including plastics, metals, wood, glass, composites, foam, and more.
As a programmable and automated process, CNC machining follows the same basic steps regardless of the specific part design. These steps include:
- Design. A design engineer creates a digital design file using computer-aided design (CAD) software. This file may go through multiple iterations to make manufacturability modifications and functional design improvements.
- Programming. The CAD design is then converted into a computer-aided manufacturing (CAM) file that can be ready by the CNC machine. This file provides the machine tool with pre-programmed instructions on the required dimensions and cuts needed.
- Machining. A machinist or operator must manually connect the various tooling required for the project. After that, the machining operations themselves are fully automated based on the instructions provided in the CAM file. The machine starts with a block of raw material, typically referred to as the workpiece or blank. Following the uploaded instructions from the digital file, the CNC machine uses various cutting processes to reduce the blank into the desired shape.
Types of CNC Machining Processes
CNC machining uses a variety of processes to remove material from the blank. The three general machining categories include drilling, milling, and turning.
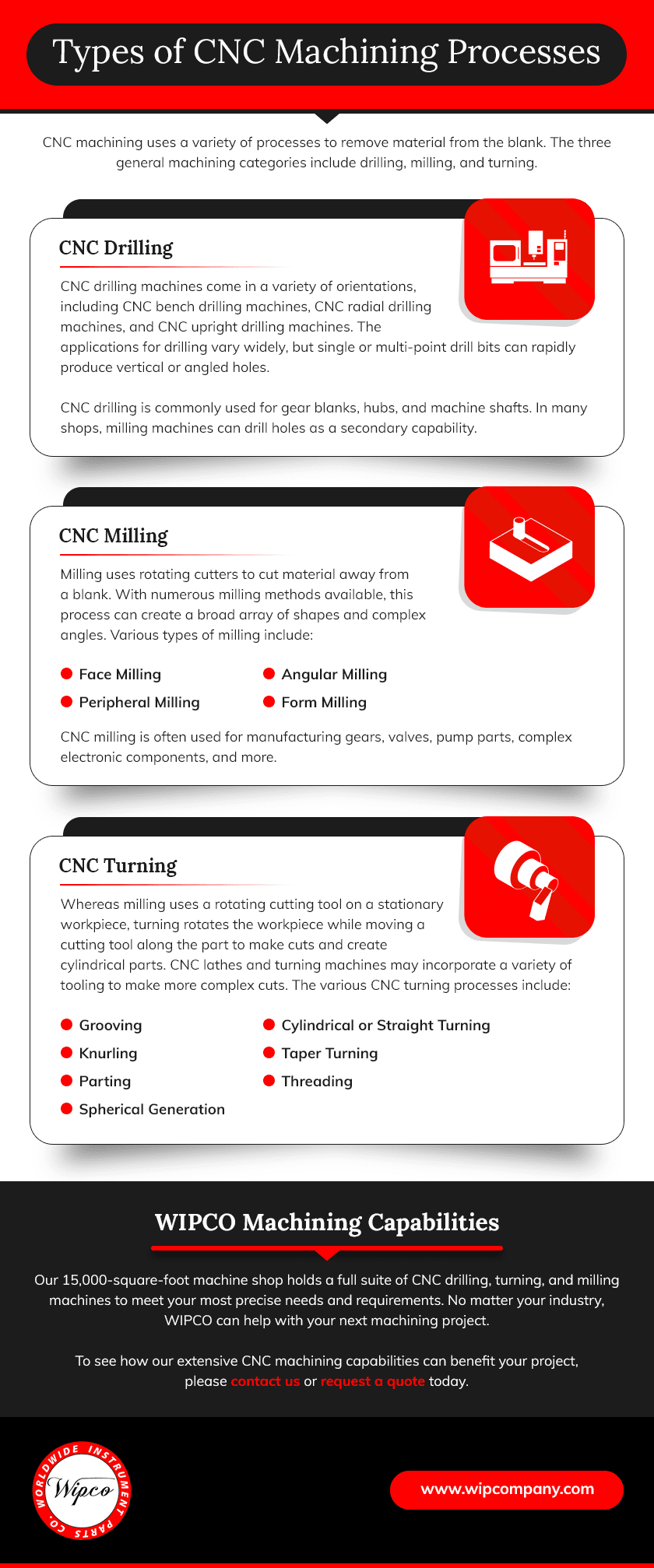
CNC Drilling
CNC drilling machines come in a variety of orientations, including CNC bench drilling machines, CNC radial drilling machines, and CNC upright drilling machines. The applications for drilling vary widely, but single or multi-point drill bits can rapidly produce vertical or angled holes.
CNC drilling is commonly used for gear blanks, hubs, and machine shafts. In many shops, milling machines can drill holes as a secondary capability.
CNC Milling
Milling uses rotating cutters to cut material away from a blank. With numerous milling methods available, this process can create a broad array of shapes and complex angles. Various types of milling include:
- Face milling – Creating flat-bottomed cavities and cutting shallow flat surfaces.
- Peripheral milling – Cutting threads, slots and other cavities, as well as deep flat surfaces.
- Angular milling – Applies the cutting tool at an angle, creating serrations, chamfers, and other angles.
- Form milling – Making spherical or circular shapes using specialized milling cutters. Common when manufacturing complex components.
CNC milling is often used for manufacturing gears, valves, pump parts, complex electronic components, and more.
CNC Turning
Whereas milling uses a rotating cutting tool on a stationary workpiece, turning rotates the workpiece while moving a cutting tool along the part to make cuts and create cylindrical parts. CNC lathes and turning machines may incorporate a variety of tooling to make more complex cuts. The various CNC turning processes include:
- Cylindrical or straight turning. Often the first step in the extended turning process, as straight turning can quickly cut and eliminate large amounts of raw material before applying other turning processes to introduce more intricate, detailed cuts.
- Grooving. A tool gets pressed into the top surface of the turning blank, creating a groove.
- Knurling. Texture gets added, often for increased ergonomics and grip in the final product, by cutting a shallow pattern into the blank.
- Parting. An entire portion of the blank material gets removed by cutting into the turning blank.
- Spherical generation. A blank is reduced to a spherical shape.
- Taper turning. The machine generates a smooth taper by slowly narrowing the diameter of the cut.
- Threading. Threads are added to cylindrical parts, such as screws, by pressing a tool into the blank to form helical grooves.
How CNC Machining is Used
A fully equipped CNC machining facility offers a great deal of versatility. This makes CNC machines a popular choice for applications across all industries that require precision machined parts. Here are just a few examples of common applications for CNC machining:
Prototyping
In advance of full production, a single physical part or small batch of parts is usually produced for testing. A project may go through numerous prototypes as design flaws or functionality issues are identified and corrected, so it’s important to use a cost-effective fabrication method for creating the prototypes. CNC machining produces prototypes without the need to fabricate expensive molds or significantly retool equipment. If the prototype requires changes, the CNC machines simply need new pre-programmed instructions to quickly build another prototype.
Tooling
CNC machining can play an adjunct role in other forms of manufacturing. For example, CNC machines are often used to create complex metal molds used in injection molding processes. A prominent example is plastic injection molding. Many of the tools used in CNC machining were themselves created using a CNC machine.
Full Scale Production
CNC machining produces high volumes of parts with an exceptional degree of accuracy and repeatability. This capability makes it well suited for high-volume production runs and blanket orders.
Custom Parts
CNC machining offers an ideal method for creating fully custom parts. The precision capabilities of CNC machining facilitate a high degree of originality in part designs. CNC machines can handle highly complex cuts and close tolerances, allowing for very strict customization of parts and components.
Many industries rely heavily on CNC machining, including:
- Aerospace. Aerospace engineers and manufacturers need the flexibility to design and produce aircraft parts that are simultaneously complex and precise, such as engine mounts and landing gears.
- Medical. CNC machining frequently meets the medical industry’s demand for very complex device components for heart rate monitors, X-ray machines, and other critical diagnostic and lifesaving equipment.
- Oil and gas. The oil and gas industry relies on CNC machining to produce valves, pistons, pipeline parts, and other safety-critical components.
- Automotive. Automobile designers and manufacturers use CNC machining for prototyping, as well as the production of interior panels, drive axles, cylinder heads, gearboxes and engine blocks.
- Electronics. The electronics industry turns to CNC machining for precise, repeatable parts with a quick turnaround. CNC machining is used for both prototyping and producing small and large components on printed circuit boards, electronics casings and enclosures, heat sinks, and more.
- Commercial. CNC machining has a variety of commercial applications for consumer products, prototyping, packaging, and more.
WIPCO Machining Capabilities
Worldwide Instrument Parts Co. (WIPCO) is an ISO 9001:2015/AS9100D-certified specialty manufacturer of precision machined parts. Our 15,000-square-foot machine shop holds a full suite of CNC drilling, turning, and milling machines to meet your most precise needs and requirements. No matter your industry, WIPCO can help with your next machining project.
To see how our extensive CNC machining capabilities can benefit your project, please contact us or request a quote today.
Established in 2000, Worldwide Instrument Parts Company (WIPCO) is a specialty manufacturer of precision machined parts. Throughout the years, our establishment has developed within the oil & gas industry along with many other sectors, fine-tuning the way we machine materials to meet specifications no matter how simple or complex. With our CNC machining capabilities, we’re able to produce high-quality parts catered to your exact needs.
Overview of CNC Machining Process
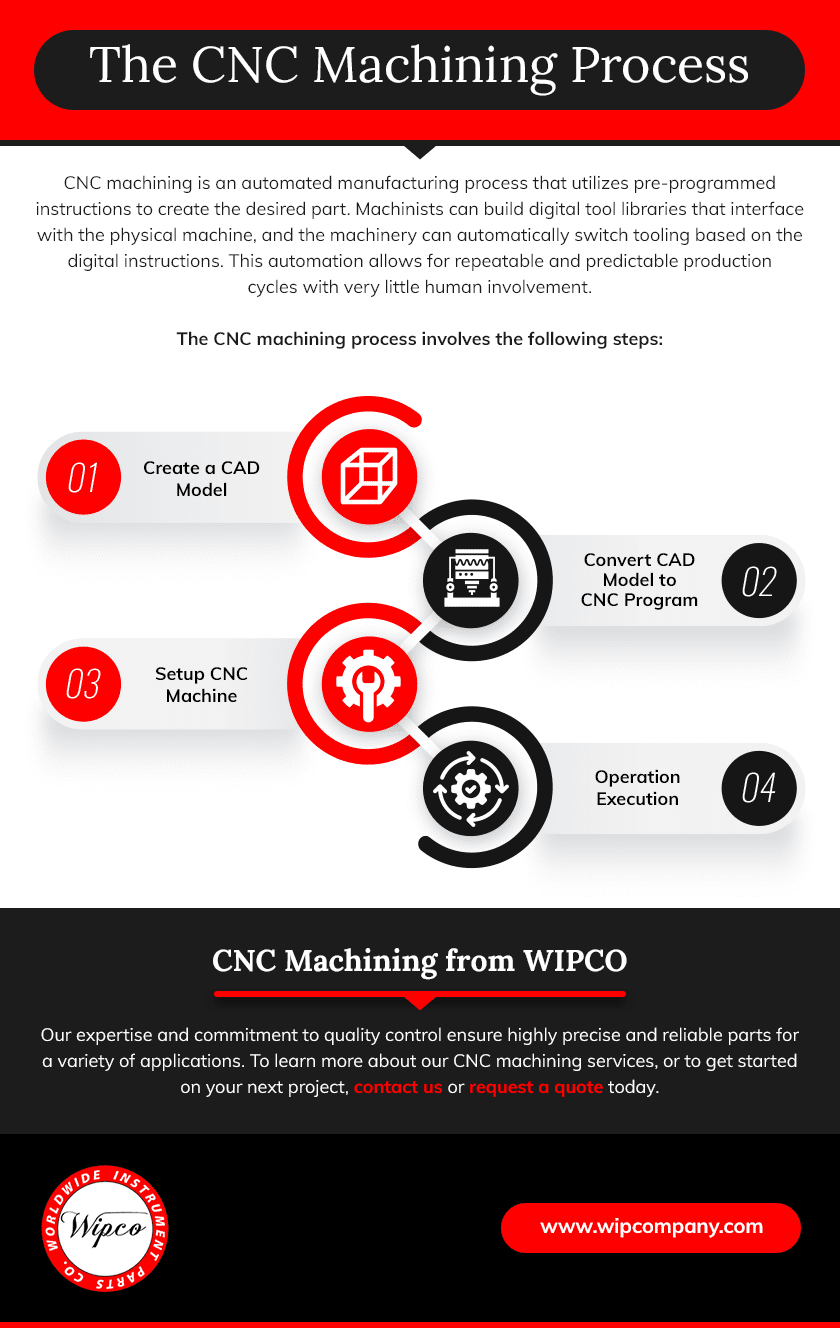
CNC machining is an automated manufacturing process that utilizes pre-programmed instructions to create the desired part. Machinists can build digital tool libraries that interface with the physical machine, and the machinery can automatically switch tooling based on the digital instructions. This automation allows for repeatable and predictable production cycles with very little human involvement.
The CNC machining process involves the following steps:
- Create a CAD model. Engineers create a 3D or 2D design of the desired part.
- Convert CAD model to CNC program. The CAD model design is exported into a compatible file format before it is converted into CNC machine instructions using CAM software.
- Setup CNC machine. Once the file is converted, the machine operator prepares the machine and workpiece.
- Operation execution. The machine operator initiates the machining program, which executes the operation and creates the designed part.
Types of CNC Machining
CNC machining encompasses various types of subtractive machining methods, each of which performs different tasks to produce the desired part. At WIPCO, we offer CNC milling, turning, and drilling services to produce parts based on customer specifications.
CNC Milling
CNC milling is the process of cutting and drilling material with a computer-controlled rotating cylindrical tool that is held in a spindle. There are four major types of milling: face, plain, angular, and form. Each style is used to create a variety of part designs and features such as slots, chamfers, threads, and pockets. CNC Milling is most commonly used to create parts for vehicles, electronic equipment, and other valuables within the medical and military fields.
CNC Turning
CNC turning is the process in which a chuck holds a bar of material, such as plastic or metal, in place. The workpiece rotates on a lathe while a computer-controlled turret with attached tooling cuts the material into the pre-programmed shape.
There are several types of CNC turning processes that can be used together to achieve the desired results. These include straight or cylindrical, grooving, taper turning, knurling, spherical generation, parting, and threading. Common applications for CNC turning include high-precision aerospace parts, dental and medical instruments, automotive parts, and more.
CNC Drilling
CNC drilling is the process of creating holes or other shapes for items such as screws and bolts. Using a spindle, an operator can control the size and diameter to drill a hole. Compared to other CNC machining types, CNC drilling is the simplest to accomplish and often requires less time.
CNC Drilling is commonly used to create plates or shields for items that cover and house important parts.
CNC Machining from WIPCO
No matter how simple or detailed your needs are when it comes to creating precision parts, WIPCO’s CNC machining services can produce high-quality components to fit your every need. Our 15,000 square-foot facility houses various state-of-the-art CNC machinery, including mills, screw machines, and lathes. Our expertise and commitment to quality control ensure highly precise and reliable parts for a variety of applications. To learn more about our CNC machining services, or to get started on your next project, contact us or request a quote today.